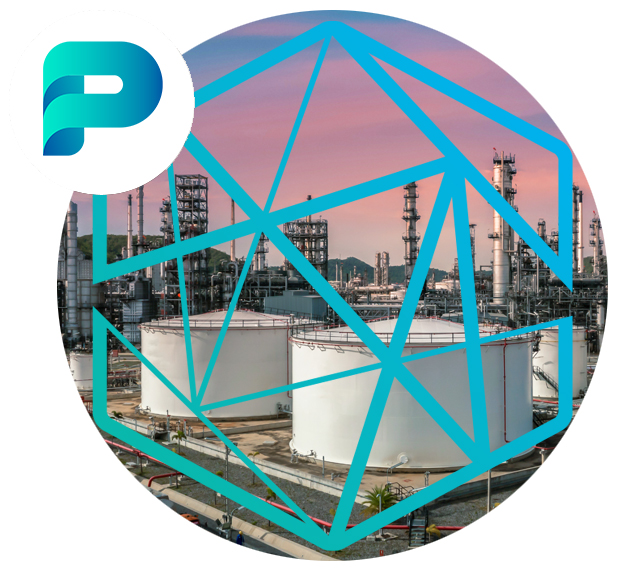
Random packing is commonly used in distillation and absorption columns to facilitate mass transfer between gas and liquid phases. The internals of a random packing column are designed to create a large surface area for intimate contact between the gas and liquid phases, allowing efficient transfer of components. Here are some common types of random packing column internals: